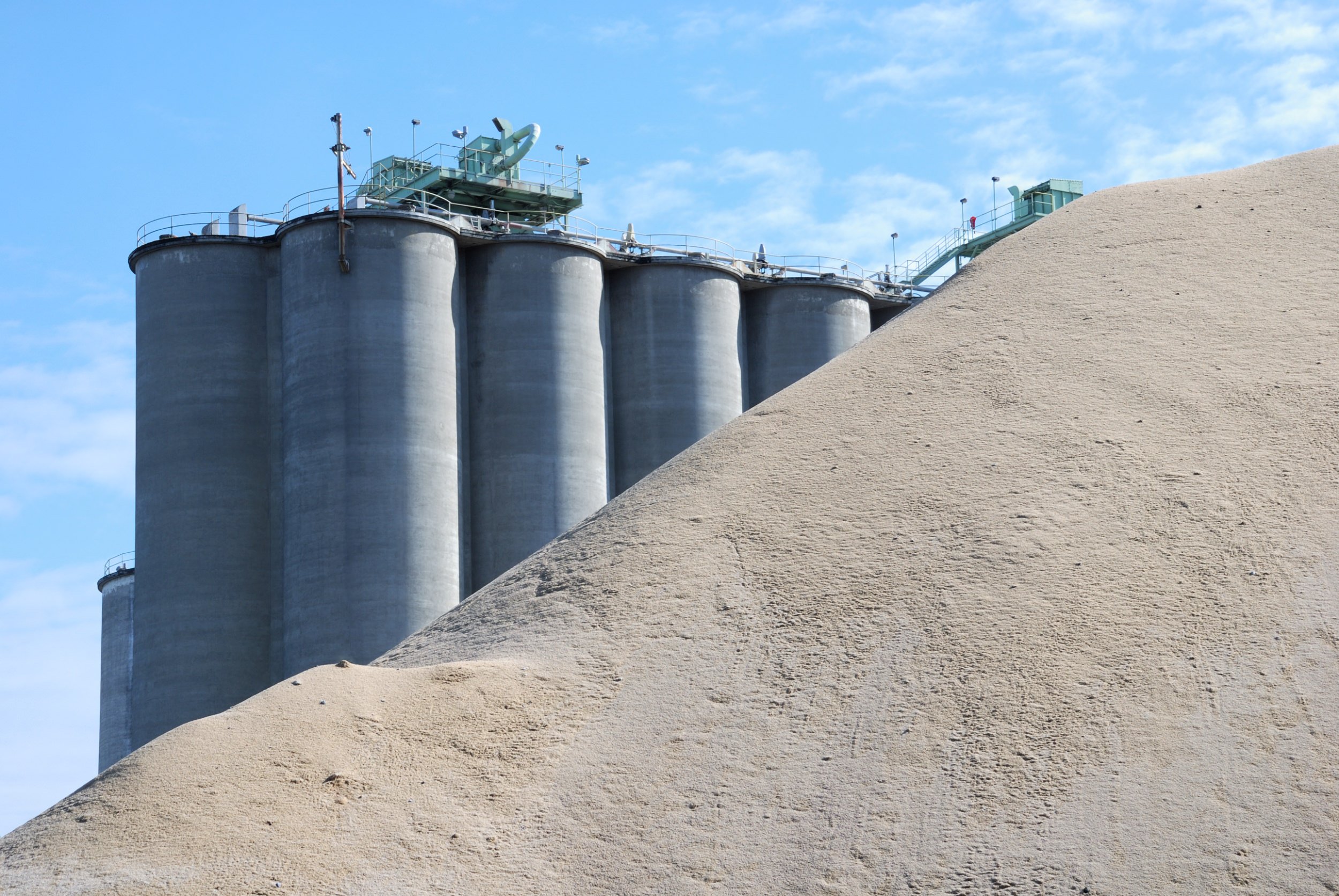
Our Solution
OUR SOLUTION
Introducing the CO₂ntainerᵀᴹ: a modular solution to industry circularity
The CO₂ntainerᵀᴹ is the realisation of our award-winning Accelerated Carbonation Technology (ACT) as a compact, mobile CCUS solution. Our innovative Plug ‘n Play system allows for seamless integration and transportation across the globe in two 40FT containers.
The CO₂ntainerᵀᴹ captures CO₂ at the source, which becomes an ingredient to carbonate industrial residues destined for landfill. The solution is able to treat up to 12,000 tonnes of residues annually in the process. Housed inside the CO₂ntainerᵀᴹ, ACT enables the production of carbonated products for the construction industry. This includes carbon negative aggregate, which has a variety of applications including in cement blocks, road filler and green roofing substrate.
MAIN FEATURES
-
CO₂ capture
Direct capture from flue stack, 1,500tonnes– 4,000tonnes CO₂ per annum
-
24,000 tonnes
Waste treated per annum
-
Seamless integration
No interference with production
-
100% automation
Manual or automatic operation
-
Cloud connected
Industry 4.0 capabilities
-
20 minutes
Safely captures and permanently stores CO₂ within 20 minutes.
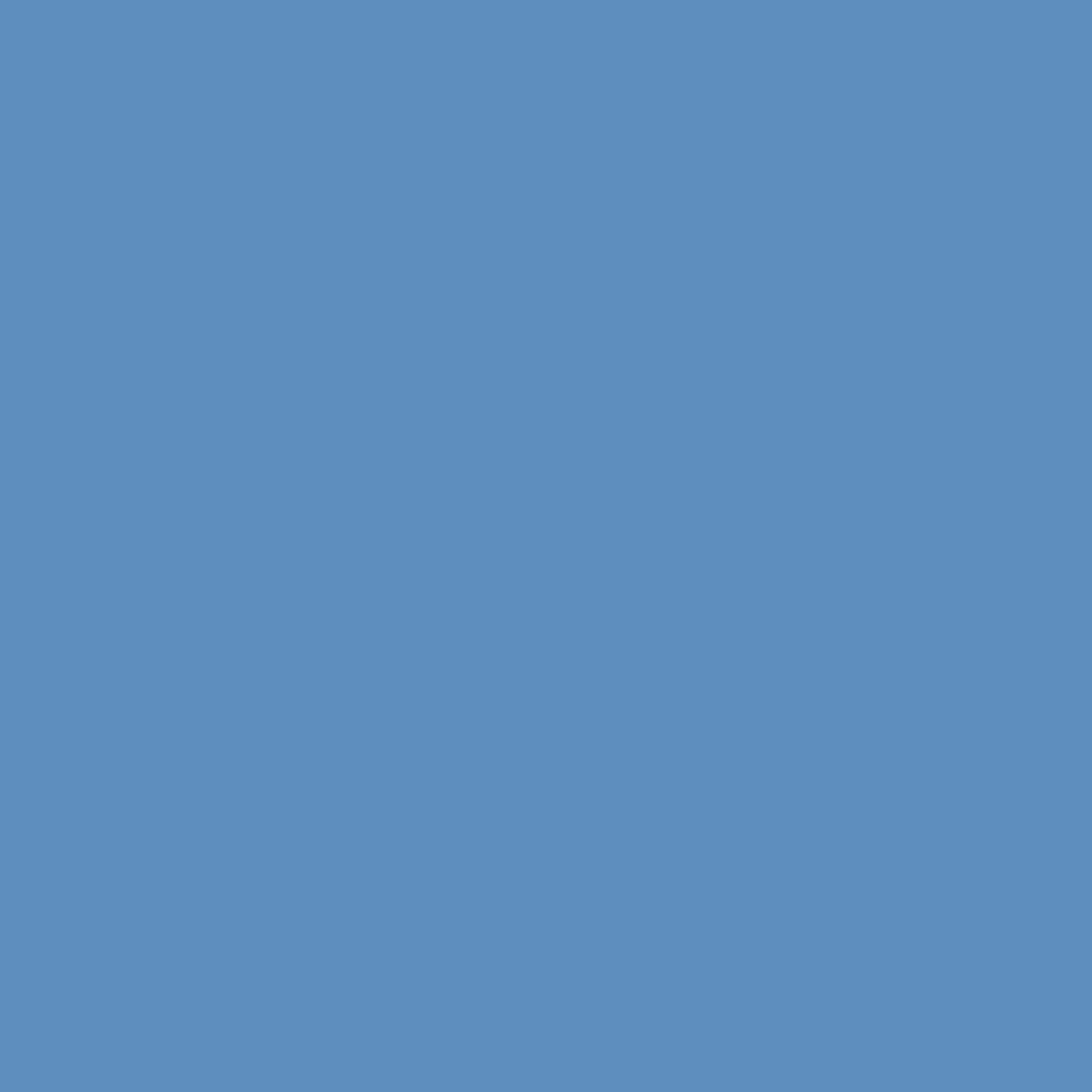
OUR SCALABLE APPROACH
Our technology can be scaled to meet the requirements of our clients. Contact us to discuss your needs.
WHAT ACCELERATED CARBONATION IS
Based on one of nature’s ways of sequestering carbon
In the natural world, this reaction is extremely slow. By engineering these conditions and exposure to CO₂, our patented solution accelerates this reaction, making it a real and ready circular solution to residues and carbon emissions.
-
Based on the natural process of carbonation
Reaction is controlled, managed and accelerated to take 15 – 20 minutes
Industrial residues contain calcium and magnesium compounds making them reactive
Metals and contaminants are stabilised
pH of residues is reduced
Exothermic, carbon-negative process
Permanent CO₂ capture
The Input and Output Process
-
CO₂ is captured directly from the flue stack without the need for pre-treatment. The captured carbon is permanently and safely stored in the manufactured materials indefinitely. Mineralisation is one of the few routes considered permanent carbon capture. The amount of carbon captured will vary depending on the reactivity of the residues treated, ranging between 10 – 30% by weight of the residue.
-
The residues produced from the site are used as a direct ingredient into the process, added to the system from a silo. Residues produced by the processes in hard to abate sectors are reactive to CO₂ and in managed conditions, can act as a carbon sink. Our expertise in carbonation and mineralisation is founded on robust science, extensive material characterisation, and the mastering the parameters of the ACT reaction. Our Scientists & Engineers have tested over 1,000 different samples across these industries, from cement bypass dust (CBD) to bottom ash (IBA), and steel slags to Air Pollution Control Residues (APCr), understanding them as a valuable ingredient to capture carbon and manufacture new materials.
-
By combining captured carbon with industrial residues, our solution manufactures CircaBuild and CircaGrow, our carbon negative alternatives to virgin aggregate and fertiliser. These new materials become inputs to a circular system, where waste products are transformed into assets.
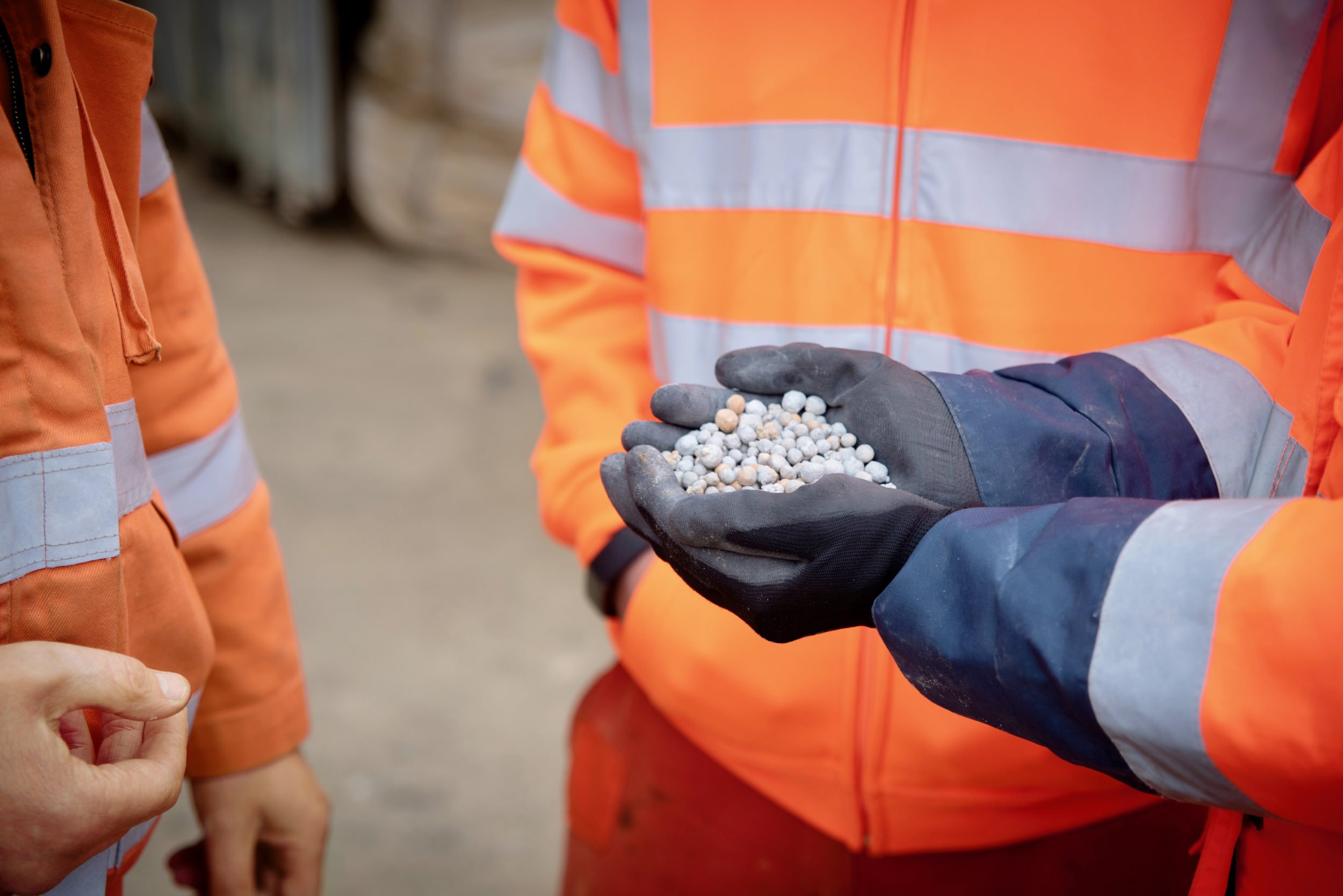
THE BENEFITS
Direct cost savings
Carbon footprint reduction
High-value manufactured products
Operational Benefits:
Smooth integration and implementation with minimal downtime
Reaction is exothermic, requiring minimal energy inputs
Engineering deployment services offered
Indisputable experts in carbonation and industrial residues
Carbon requires no pretreatment or purification
Small space footprint required
Landfill-destined residues are valorised, given a new life
Sustainable materials manufactured onsite for integration or revenue generation
Real and ready solution, available now
Adaptable to client site, residues and needs
HOW IT WORKS
The Reaction
The carbonation reaction primarily involves metal/mineral oxides, hydroxides and silicates, principally those of calcium and magnesium, reacting with CO₂ gas. If the reaction conditions are controlled, carbonation can be achieved in minutes instead of in the years taken for the natural reaction. Calcium and magnesium carbonates, on account of the environmental impact and stability, are the favoured reaction products, and are simply represented as Ca in the reactions below:
Ca(OH)₂ + CO₂ → CaCO₃ + H₂O